A193 B8M STUD BOLTS MANUFACTURER IN CHINA
A193 B8M stud bolts are a specific type of fastener used in various industries, known for their corrosion resistance and mechanical properties in high-temperature and high-pressure environments. Let me break down the components of the name:
1. A193:This refers to the ASTM A193 specification, which covers various types of alloy steel and stainless steel bolting materials for high-temperature or high-pressure service. The specification includes different grades with varying properties.
2. B8M: The “B8M” is a specific grade within the ASTM A193 specification. It specifically designates a stud bolt made from stainless steel alloy grade 316, also known as B8M Class 1 or B8M Class 2.
Stainless steel grade B8M (Type 316) is an austenitic chromium-nickel stainless steel alloy that contains molybdenum, which enhances its corrosion resistance, especially in chloride-rich environments. Due to its resistance to corrosion and good mechanical properties, B8M stud bolts are commonly used in applications where exposure to corrosive chemicals, seawater, and high temperatures is a concern. Such applications can include industries like petrochemical, chemical processing, marine, and more.
These stud bolts are threaded rods with threads on both ends and are often used with nuts to secure components together in various assemblies. They play a vital role in maintaining the integrity of structures and equipment operating in demanding conditions.
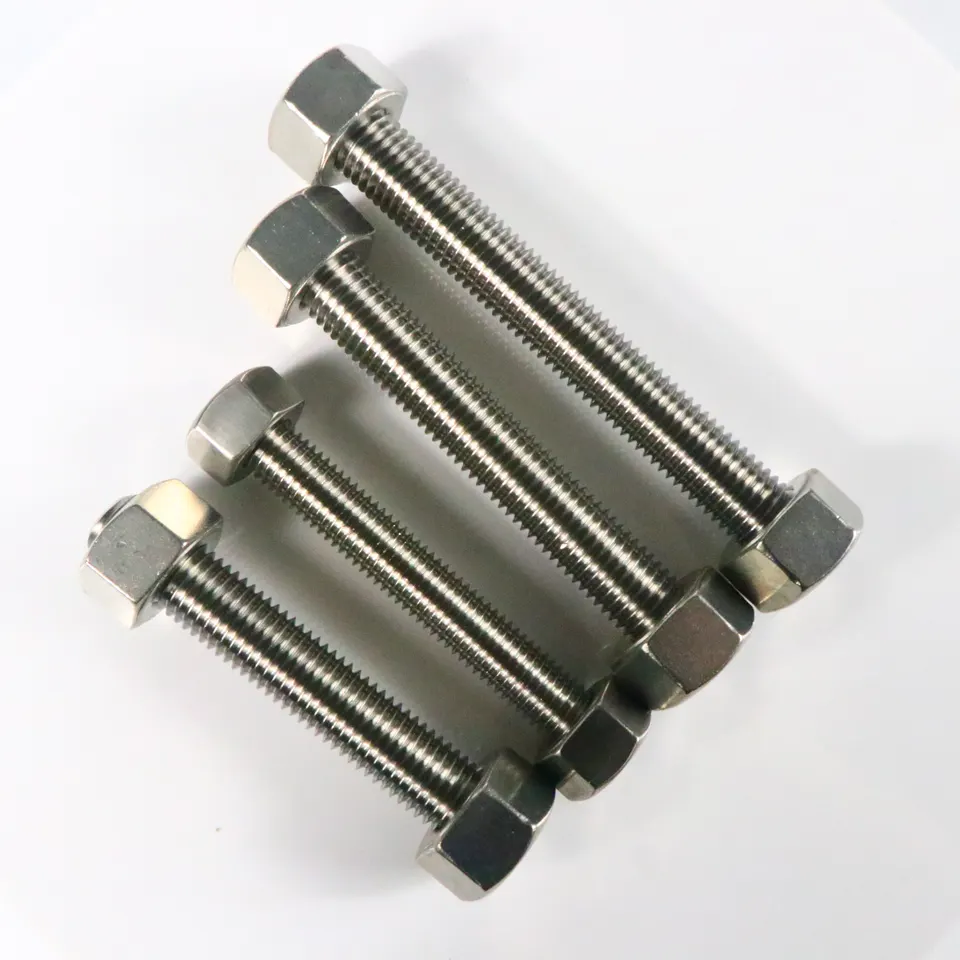
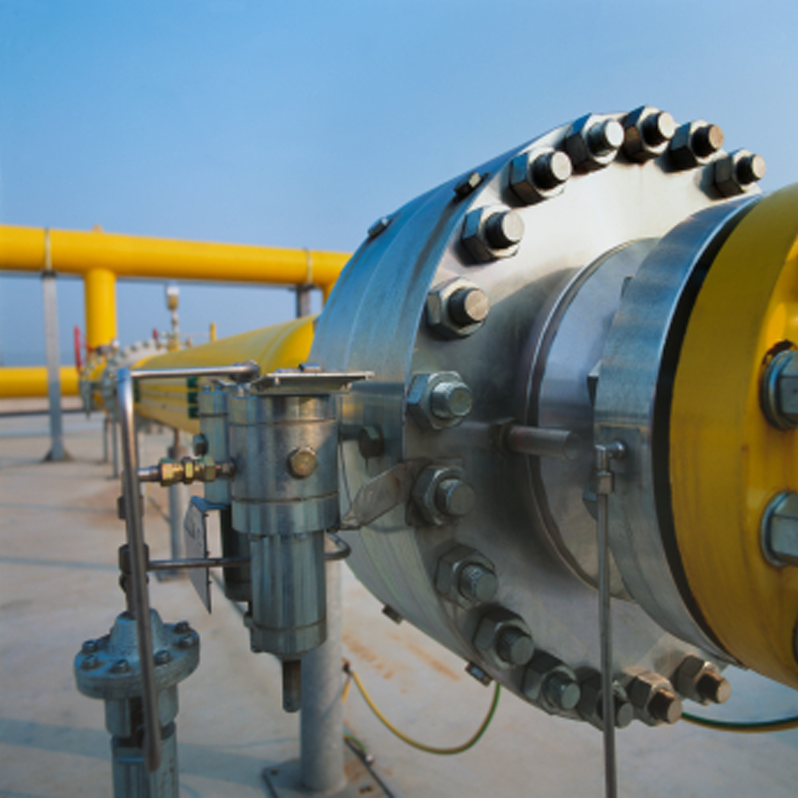
Specification of A193 B8M stud bolts:
A193 B8M stud bolts, made from stainless steel grade 316, find applications in various industries due to their corrosion resistance and mechanical properties. Here are some common applications:
Product name | ASTM A193 B8M Stud Bolts |
---|---|
Diameter | 1/4″ – 4″ |
Dimension Standard | ASME B18.31.2 |
Thread | UNC/UNF/8UN |
Material | Stainless steel, AISI 316 |
Compatible nuts/washers | A194 GR.8M heavy hex nuts |
Manufacturing Process | wire drawing, thread rolling, heat treatment, surface treatment |
Surface treatment | Black Oxide Coating/Zinc Plating (Electroplating)/Hot-Dip Galvanizing/Mechanical Galvanizing/Dacromet Coating/Painting or Powder Coating |
Application Industry | Piping Systems/Pressure Vessels/Pressure Vessels/Oil and Gas Industry/Power Generation/Chemical Processing |
A193 B8M stud bolts are specifically chosen for their corrosion resistance and mechanical properties in challenging conditions. Always ensure that the selected fasteners meet the requirements of your specific application to ensure safety and reliability.
Chemical Composition:
Elements | Range | Allowed Variation, % |
---|---|---|
Carbon, max | 0.08 % | + 0.01 |
Manganese, max | 2.00 % | + 0.04 |
Phosphorus, max | 0.045 % | + 0.010 |
Sulfur, max | 0.030 % | + 0.005 |
Silicon, max | 1.00 % | + 0.05 |
Chromium | 16.00 – 18.00 % | +/- 0.20 |
Nickel | 10.00 – 14.00 % | +/- 0.15 |
Molybdenum | 2.00 – 3.00 % | +/- 0.10 |
Mechanical and physical properties:
Mechanical Requirements, Inch Products | |||||||
---|---|---|---|---|---|---|---|
Class | Diameter | Tensile Strength, min, ksi | Yield Strength, min, ksi | Elongation in 4D min, % | Reduction of Area, min, % | Hardness, max | |
1 | All Diameters | 75 | 30 | 30 | 50 | 223 HBW | 96 HRB |
2 | 3/4 and under | 110 | 95 | 15 | 45 | 321 HBW | 35 HRC |
Over ¾ to 1, incl. | 100 | 80 | 20 | 45 | |||
Over 1 to 1-1/4, incl. | 95 | 65 | 25 | 45 | |||
Over 1-1/4 to 1-1/2, incl. | 90 | 50 | 30 | 45 |
Quality control of A193 B8M Stud bolts:
Control Method | Detail |
---|---|
Material Inspection: | Verify the material's composition, heat treatment, and quality upon receipt. Conduct metallurgical analysis to ensure the material properties meet the standards. |
Process Control: | Implement strict process control measures for heat treatment, machining, threading, and any other manufacturing steps. Maintain consistent process parameters to ensure uniform quality. |
Inspection Points: | Introduce inspection points at various stages of manufacturing to check for defects, dimensions, and quality. Inspect threading, dimensions, surface finish, and other critical parameters. |
Sampling and Testing: | Regularly sample products for testing, such as tensile testing, hardness testing, and metallurgical analysis, to ensure they meet the required specifications. |
Thread Inspection: | Thoroughly inspect threading using proper thread gauges to ensure accurate dimensions and fit with mating components. |
Traceability: | Implement a traceability system to track each fasteners journey from raw material to final product. This aids in accountability and recalls if necessary. |