Swaged Hose Fittings Manufacturer In China
Ningbo Teng Qi Fasteners Co., Ltd is a leading swaged hose fitting manufacturer in China. Swaged hose fittings, are components used in hydraulic systems to securely connect hydraulic hoses to various hydraulic components such as pumps, valves, cylinders, and other equipment. These fittings are designed to create a permanent and leak-proof connection between the hydraulic hose and the fitting. The process of swaging involves crimping the fitting onto the hose using a hydraulic crimper machine. During this process, the fitting is compressed tightly around the hose, creating a strong mechanical bond. The crimping process typically deforms the fitting’s collar around the hose, providing a secure grip that prevents the hose from slipping or leaking under pressure.
Swaged hose fittings come in a variety of shapes, sizes, and configurations to accommodate different types of hydraulic hoses and applications. They are widely used in industries such as construction, agriculture, automotive, manufacturing, and more, where hydraulic systems are prevalent.
The advantages of swaged hose fittings include their reliability, durability, and ability to withstand high pressure. Additionally, these fittings provide a smooth internal surface, minimizing fluid turbulence and pressure drop within the hydraulic system, which is crucial for maintaining system efficiency. Swaged fittings are known for their superior performance and are widely used in critical hydraulic applications where secure connections are essential.
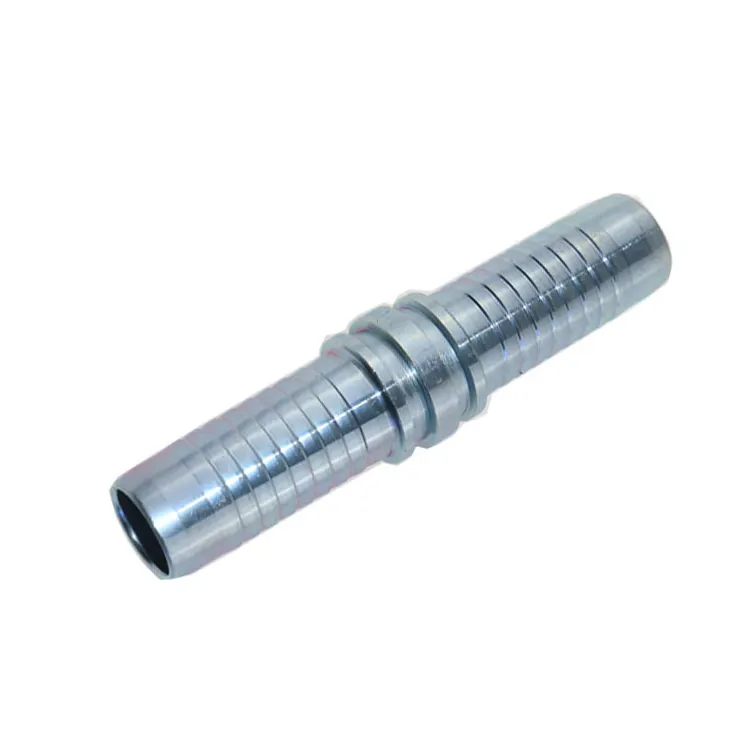
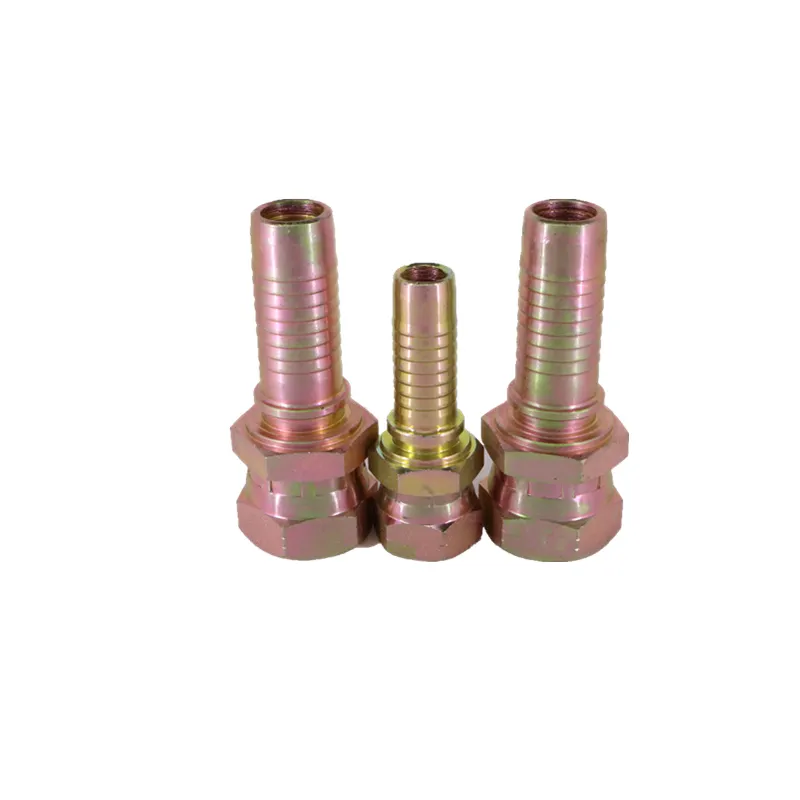
Choose the right swaged hose fitting:
Choosing the right swaged hose fitting involves considering various factors. Firstly, one must take into account the diverse materials from which these fittings can be crafted, including carbon steel, stainless steel, brass, and aluminum. These materials offer different levels of durability and corrosion resistance. Surface treatments, such as zinc plating, ZiNi plating, and customized plating, further enhance the fittings’ ability to withstand corrosion, sometimes for up to 1000 hours.
Additionally, swaged hose fittings come in a plethora of standards and thread forms, catering to different industry requirements. Some widely used standards include JIC (Joint Industry Council), NPT (National Pipe Thread), BSPP (British Standard Pipe Parallel), ORFS (O-ring Face Seal), Metric, JIS (Japanese Industrial Standard), and Code 61 62 Flanges. Each standard serves specific purposes and applications, so understanding the specific needs of your hydraulic system is crucial in making an informed choice.
Furthermore, the configuration of swaged hose fittings can vary. They can be one-piece fittings, ready to use for hose assemblies after crimping, or two-piece fittings that are crimped with the hose to create hose assemblies. This choice depends on the complexity of the hydraulic system and the ease of assembly required.
When identifying the appropriate swaged hose fitting, it’s essential to pay attention to part numbers. Fittings ending with ‘1’ are designed for one and two wire braid hoses, while those ending with ‘2’ are meant for four wire spiral hoses. Generally, ‘1’ is suitable for sizes ranging from 1/8 inch to 5/8 inch, whereas ‘2’ is ideal for sizes from 3/4 inch to 2 inches. The key difference lies in the tail length, with ‘2’ having a longer tail, providing enhanced stability and grip when crimped with the hose.
In summary, the right swaged hose fitting selection involves understanding the material options, considering industry standards, choosing between one-piece and two-piece fittings, and paying attention to part number endings for compatibility with specific hose sizes. Careful consideration of these factors ensures a secure, durable, and efficient hydraulic system.
FAQ about Swaged Hose Fittings:
1.What makes your swaged hose ferrules stand out in the market?
Our swaged hose ferrules are synonymous with exceptional quality and unmatched durability. Crafted with precision, our ferrules are designed to meet stringent industry standards, ensuring reliable performance in diverse applications. We pride ourselves on delivering products that exceed customer expectations.
2.How does the quality of your swaged hose ferrules benefit customers?
The superior quality of our swaged hose ferrules translates into long-lasting, dependable solutions for our customers. By choosing our ferrules, customers experience reduced downtime, minimized maintenance, and enhanced safety in their hydraulic systems. Quality is the cornerstone of our manufacturing process, ensuring customer satisfaction and peace of mind.
3.Can you elaborate on the competitive pricing of your swaged hose ferrules?
Despite our unwavering commitment to quality, we offer competitive prices that provide exceptional value to our customers. Through streamlined manufacturing processes and strategic sourcing, we maintain affordability without compromising on the integrity of our products. Our competitive pricing allows customers to optimize their budgets while enjoying top-tier ferrules.
4. What assurance do customers have regarding the reliability of your swaged hose ferrules?
How are hydraulic hose fittings tested for quality and performance?
5. How do your competitive prices contribute to customer savings?
Our competitive prices are designed to deliver tangible savings to our customers. By choosing our affordable swaged hose ferrules, customers can optimize their budgets, leading to reduced operational costs and increased profitability. The combination of quality and affordability ensures long-term savings and customer satisfaction.
Manufacturer quality control of Hydraulic hose fitting:
Material Inspection: | Verify the material’s composition, and quality upon receipt. Conduct metallurgical analysis to ensure the material properties meet the standards. |
Process Control: | Implement strict process control measures for machining, threading, and any other manufacturing steps. Maintain consistent process parameters to ensure uniform quality. |
Equipment Calibration: | Regularly calibrate manufacturing equipment to ensure accurate measurements and consistent results. |
Inspection Points: | Introduce inspection points at various stages of manufacturing to check for defects, dimensions, and quality. Inspect threading, dimensions, surface finish, and other critical parameters. |
Sampling and Testing: | Regularly sample products for testing, such as tensile testing, hardness testing, and metallurgical analysis, to ensure they meet the required specifications. |
Non-Destructive Testing (NDT): | Implement NDT methods like ultrasonic or magnetic particle testing to detect hidden defects. |
Thread Inspection: | Thoroughly inspect threading using proper thread gauges to ensure accurate dimensions and fit with mating components. |
Traceability: | Implement a traceability system to track each fasteners journey from raw material to final product. This aids in accountability and recalls if necessary. |